Sanitaryware - Sanitary ware
Leading Exporters of Bathoom Sanitary Ware, Brand " SONA", Wide Range & Best Quality, Attractive Price, Timely Delivery - details see: https://www.buildingsupplieshub.com/sanitaryware-10015004
Place of Origin: Gujarat India | Brand Name: SONA | Model Number: Sanitary ware | Material: Ceramic |
Structure: One Piece | Installation Type: Floor Mounted |
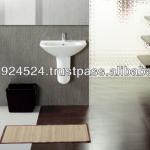
Technical Specifications
Specifications of 'SONA SANITARY WARE' Products
Charactristics | IS 2556-1-1994 | SONA' Test Value |
Surface Blemish | Should conform to Norms | In conformity with the Norms |
Water Absorption % | 0.5 Max. Mean Value | 0.1 Max. Mean Value |
Modulus of rupture (M.O.R.) | 60 Mpa Min. Mean Value | 70 Mpa Min. Mean Value |
Crazing Resistance 0.34- 0.37 Mpa | 10 Hrs. Min. | 20 Hrs. Min. |
Chemical Resistance | Should Conform to Norms | In Conformity with the Norms |
Staining & Burning Resistance | Should Conform to Norms | In Conformity with the Norms |
INSTALLATION & MAINTENANCE TIPS
- Install Wash Basins with or without pedestals on CI Bracket with Rag Bolts. If wash basin is Large in size install on pedestal screwed to the floor.
- Install wall mounting E.W.C. With the help of CI chair.
- Install Floor Mounting E.W.C. Screwed to the floor.
- Avoid using Cement at the hollow bottom portion of E.W.C.
- Regular Cleaning with dry cloth / Mild Detergent is recommended to avoid stains & if required diluted Hydrochloric acid may be Used.
- Do not use hard bristled brush for cleaning so as to avoid scratches.
Your Trouble-Shooting Guide
(FOR GOLD - TYPE FITTINGS)
At Ceramics Division, SONA Ceramics, it has been our endeavour not only to provide you with the best possible service, but also to help you serve your customers better. We have been analysing the complaints received by us and have discovered that most of the complaints fall into a pattern. We would like to share the qualitative results of the analysis with you, so that you can be better prepared to handle any complaints received from your customers.
For each problem faced, the probable causes are explained. Alongside, you can find the corrective actions required to solve these problems. We hope that you would find this trouble-shooting chart useful. You could apply this for suites as well as wallvit pans
Flushing Test
1 Toilet Paper Test
The water closet shall be filled with water to its normal water seal level and charged with six pieces of usual toilet paper or polythene sheet of 0.05 mm thickness approximately 150 mm x 115 mm in size and loosely crumpled. It shall then be flushed. This test shall be repeated four times and the pan shall discharge the full charge of the paper at last three out of four times.
2 Smudge Test
The whole of the interior surface of water closet to 40 mm below the flushing rim shall be smudged with quartz powder of contrasting colour passing through 1.18 mm IS sieve and shall then be flushed observing carefully the surface of the water closet during the flushing. Immediately after the flushing, there shall be no smudge left on the bowl.
3 Holding Capacity Test
The water closet when sealed at the outlet and vent (if fitted) with water-tight seal shall be capable of holding not less than 10 1 of water between the normal water level and the highest possible water level of the water closet as installed.
4 Ball Test
Single Ball Test :The ball shall be made of non-absorbent material. The relative density of the ball shall be between 1.075 and 1.080. The diameter of the ball shall be 43 ± 0.5 mm. Place the ball into the water closet to be tested and then flush the water closet. The ball shall be discharged in the normal manner.
The outlet (trap) of the water closet goes into the floor. The outlet (trap) of the water closet goes into the wall. | 5 Fifty Ball Test Fifty balls of non-absorbent material, having a mass each of 3.7 ± 0.1 g, and a diameter of 20 ± 0.1 mm shall be dropped into the water closet bowl and flushed. Repeat the test five times. A minimum of 85 percent of all balls should be flushed out in the five tests. 6 Load Bearing Test force of 4 + ° .05 kN shall be applied for period of one hour by placing it on a wooden beam with a cross section of 100 mm x 100 mm positioned across the centre of the opening of the top surface of the WC. There shall be no damage or defect which shall occur to the WC. 7 Saw Dust Test Specification of the Saw Dust 20 g of dry saw dust test sifted through 2 mm sieve. Procedure: Set up the WC, cistern or flush valve and flush pipe (if required) as specified by the manufacturer. Charge the WC with water to its designed water seal level. Fully wet the entire internal surface of the WC below the rim. Sprinkle 20 g of fine dry saw dust of above specification on the inside of the WC between the normal water level and the flushing rim as completely and evenly as possible. Then flush the WC. The sprinkle saw dust should be cleaned below 40 mm of rim of WC. 8 Splash Test Procedure: Set up the WC, cistern or flush valve and flush pipe (if required) as specified by the manufacturer. Charge the WC with coloured water to its design water seal level. Ensure that the floor area is cleaned and dry where the splash test to be carried out. Activate the flush valve or cistern to the discharge the WC. Observe and record whether flushing water splashed over rim onto the floor. Repeat the test 5 times. Record whether the flushing water splash over the rim onto the floor. Isolated droplets up to 10 Nos., shall not be the cause for rejection. |
Problem faced | Probable Reasons | Corrective Action |
Tank is shaking | Expansion plug may not be correctly fixed in the tank's fixing hole provided towards the back of the closet. | Fix the expansion plug provided. |
Tank holding screw may not be tightened fully. | Tighten the tank holding screw evenly till it cannot be tightened any further with one hand. | |
Continuous leakage of water from the cistern | Arm may be fixed in a wrong direction. | Fix the arm such that the shorter arm side is facing the front of the cistern. |
Valve ring may not be fixed properly to the bottom of the body. | Fix the valve ring to the top of the groove provided in the body. Ensure that the valve ring sits securely around the groove. | |
Valve ring may have cracked or could be worn out. | Replace the valve ring. | |
Lifting rod and floating body assembly may not be perpendicular. | Adjust the bracket so that its center hole aligns with the hole provided in the lid of the cistern. | |
Lifting rod and floating body assembly may not be guided through the guide hole provided in the bottom of the valve seat. | Guide the lifting rod through the hole provided in the bottom of the valve seat. | |
Cistern not fully tightened to the closet. | Tighten tank holding screws evenly till they cannot be tightened further with one hand. | |
Discharge of water stops abruptly when the flush knob is pulled and released | Water may be overflowing through the floating body. | Turn the adjusting screw provided on the top of the inlet in the anti clockwise direction. Reduce the water level such that the water level shuts off below the 'over-flow' level. |
Buoyancy may not be created for the floating body. | 1. Push stop dog (black rubber tube) which is fixed to the lifting rod such that top end of the stop dog touches the bottom of the lifting bar. | |
2. Adjust the lifting bar such that the hole provided near the top-end threaded portion of the lifting-bar is just visible over the lid screw (when observed in assembled condition). | ||
Water does not enter the cistern through the inlet | The inlet may be in the fully closed position. | Turn the adjusting screw provided on the top of the inlet in the clockwise direction to open the inlet. |
Water line may be choked. | Ensure periodical cleaning of water tank and water lines. | |
Water quantity insufficient for effective flushing | Float ball height adjusted to lower quantity of water discharge. | Turn the adjusting screw provided on the top of the inlet in clock wise direction to increase the discharge level. (Caution: The water level may be increased till the water from the inlet shuts off at the 'top-line' mark provided on the floating body). |
Water leakage observed between cistern and closet during flushing. | Water divider may not be properly fixed. | Fix the water divider such that the 2 weep holes provided in it face each other after installation. Ensure that the inlet of the water divider is passing through the outlet of\ the valve-seat fully |
Continuous innovation and improvement in manufacturing techniques and products are carried out regularly. We reserve the right to supply articles which may not correspond exactly with the particulars given in this booklet.
Packaging Detail:Standard Box Packing and Cartoon Packing As Per Requirement |
Delivery Detail:15 Days |