OSB(Oriented strand board),osb board,osb3 - OSB/2
Type: Flakeboards | Place of Origin: Shandong China (Mainland) | Brand Name: Huicai | Model Number: OSB/2 |
Material: Wood | Usage: Outdoor | Surface Finishing: Unfinished | Grade: Excellent |
Slab Structure: Oriented Strand Boards(OSB) | thickness: 6-40mm | size: 1220*2440 |
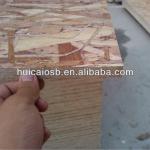
|
Oriented strand board (OSB) is an engineered wood particle board formed by layering strands (flakes) of wood in specific orientations. It may have a rough and variegated surface with the individual strips of around 2.5 × 15 cm (1" x 6"), lying unevenly across each other.
Uses
OSB is a material with high mechanical properties that make it particularly suitable for load-bearing applications in construction. The most common uses are as sheathing in walls, flooring, and roof decking. For exterior wall applications, panels are available with a radiant-barrier layer pre-laminated to one side; this eases installation and increases energy performance of the building envelope. OSB also sees some use in furniture production.
OSB2 is a precision-engineered board for structural use in load bearing dry conditions. It is a versatile alternative to plywood, it is ideal for a variety of uses from site hoarding to display stands, sheds to shelving.
OSB3 is a precision-engineered structural board for use in load bearing humid conditions. OSB3 is suitable for: Timber frame housing; Flat and pitched roofs; Wall sheathing; Flooring; Portable buildings; Caravans; and Agricultural buildings.
Manufacturing
Oriented strand board is manufactured in wide mats from cross-oriented layers of thin, rectangular wooden strips compressed and bonded together with wax and synthetic resin adhesives (95% wood, 5% wax and resin). The layers are created by shredding the wood into strips, which are sifted and then oriented on a belt or wire cauls. The mat is made in a forming line. Wood strips on the external layers are aligned to the panel's strength axis, while internal layers are perpendicular. The number of layers placed is determined partly by the thickness of the panel but is limited by the equipment installed at the manufacturing site. Individual layers can also vary in thickness to give different finished panel thicknesses (typically, a 15 cm layer will produce a 15 mm panel thickness). The mat is placed in a thermal press to compress the flakes and bond them by heat activation and curing of the resin that has been coated on the flakes. Individual panels are then cut from the mats into finished sizes. Most of the world's OSB is made in the United States and Canada in large production facilities. The largest production facilities can make over a million square feet of OSB per day.
Properties
Adjustments to the manufacturing process can impart differences in thickness, panel size, strength, and rigidity. OSB panels have no internal gaps or voids, and are water-resistant, although they do require additional membranes to achieve impermeability to water and are not recommended for exterior use. The finished product has properties similar to plywood, but is uniform and cheaper. When tested to failure, OSB has a greater load-bearing capacity than milled wood panels. It has replaced plywood in many environments, especially the North American structural panel market.
While OSB does not have a continuous grain like a natural wood, it does have an axis along which its strength is greatest. This can be seen by observing the alignment of the surface wood chips. The most accurate method for determining the axis of strength is to examine the ink stamps placed on the wood by the manufacturer.
All wood-based structural use panels can be cut and installed with the same ease and types of equipment used with solid wood.
Some manufacturers treat the wood chips with various borate compounds which are toxic to termites, wood boring beetles, molds, and fungi, but not mammals in applied doses.
Environmental impact
Emission levels of formaldehyde have been found to be not more than 10% of the criteria of key national standards.
Packaging Detail:Outer packed by the cardboard or thin plywood, inner packed by the plastic bags, strengthen by the steel or PVC tapes. |
Delivery Detail:Within 15 days after receiving T/T deposit or original L/C |