Natural strawberry translucent hematite quartz stone - 945
Type: Other Natural Stone | Place of Origin: Kazakhstan | Brand Name: Splendor | Model Number: 945 |
stone quartz: natural translucent |
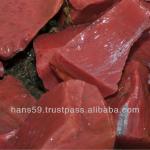
Clean natural strawvberry alabaster look alike translucent exotic stone, very rare to find.
Translucent stone
Our company is worldwide network of mining companies with own quarries, specilised in the natural translucent stones like fine alabaster, onyx or other semi precious .
We have two main product facilities for the manufacturing of translucent stone panels like 1-2 cm alabaster or the new translucent granite and marble. At factory we have 10 gang saws, 5 waterjet cutting and 2 six edged diamond wire cutting machines apart from the polishing and edge machines. We laminate upon international glass safety standards.
Stone veneer is used as a protective and decorative covering for exterior or interior horizontal and vertical walls and surfaces. The veneer is typically 1-2 mm thick and must weight less than 5 kg/m²) so that no additional structural supports will be required except glass.. Manufactured stone veneer is a decorative building material manufactured to enhance the translucent look of natural stone. The names translucent stone, stacked stone veneer, manufactured stone, and flexible stone veneer are also used for stone veneer.
We make stone veneer backed with tempered white glass with any natural stone.
Natural stone veneer is made from real stone that is either collected i.e. fieldstone, or from quarried stone. The stone is cut to a consistent thickness and weight for use as a veneer. This stone is often called thin stone veneer.
Translucent flexible stone veneer is fabricated by pulling a thin layer of stone from a slab of slate, granite, marble, sandstone, or mica schist to a glass back up.
The advantages of our manufactured natural translucent stone veneer over usual slab natural stone are:
• Extreme low cost (cost of material, cost of application, waste cost)
• Extreme low weight (ease and cost of application)
• Extreme variety of designs and colors
Manufactured translucent stone veneer is cheaper than natural stone, approximately 1/2 the cost of natural stone. Its light weight eliminates the need for wall ties or footings and make it easier and cheaper to build translucent facades. Furthermore, manufactured translucent stone veneer has a significantly smaller waste factor than natural stone but above all the variety of designs and colors makes available options which would not be possible with usual slab natural stone, since natural stone like granite or marble is not translucent at slab 2 cm level.
Thin stone veneer was first developed in the late 19th century, but there were materials developed much earlier that foreshadowed the use of stone veneer. Parts of the Roman Coliseum were made out of marble veneer that can no longer be seen.
In fact, the holes in structure of the Coliseum are from the anchors of the veneer panels. Structures throughout the Thin stone veneer was first developed in the late 19th century, but there were materials developed much earlier that foreshadowed the use of stone veneer. Parts of the Roman Coliseum were made out of marble veneer that can no longer be seen.
In fact, the holes in structure of the Coliseum are from the anchors of the veneer panels. Structures throughout the Roman Empire were made in part out of stone blocks, including the Segovia aqueduct in Spain, which was made out of granite blocks
Modern non translucent stone veneer first made its appearance in the late 1800s. The oldest of modern stone veneer product is now disintegrating. It was cut into thick portions and then hand tooled into the appropriate panels; the stones that were used were “granite, marble, travertine, limestone, and slate.” Early in its development, thin stone veneer only had the capabilities to be utilized in areas such as the inside of buildings, street-level facades and storefronts.
5 cm became the common thickness of non translucent stone veneer in the 1930s. Panels of stone veneer were generally installed via mortar techniques, with steel rods drilled into the edges of panels providing support. The utilization of thin stone veneer for complete facades of buildings popped up in the 1940s. Stone veneer construction became much of what we see today in the 1950s. Transportation improved, so stone veneer was transported more efficiently and at lower costs than ever before. Methods to attach veneer to steel were developed; diamond-bladed tools became popular for developing thin stone veneer, while elastomeric sealant began to replace mortar techniques in the construction process. Thin stone veneer in the 1960s became more of a standardized look – in fact, standard education on stone veneer became available in The Marble Engineering Handbook and Marble-Faced Precast Panels, which were published by the Marble Institute of America and National Association of Marble producers.As non translucent stone veneer panels got thinner in the 1960s, the properties of the stone used became more important in order to compensate (as did safety considerations). Concrete as an aid to stone veneer continued to develop, as “in order to eliminate bowing, cracking, and staining of the veneer.”“Diamond-studded cables” were used to cut Italian marble into the necessary slabs as a part of an era of specialization in the 1970s. A 1976 patent shows that the stone material of composite stone veneer could be finished and developed in such a fashion that “it does not have the appearance of being a part of a composite stone veneered product.” This was the beginning of developing the translucent stoneglass too.The thickness of non translucent stone veneer was able to be cut to a thickness of 3mm in the 1980s because of improvements in technology. The thickness of typical thin stone veneer was three centimeters by the early 2000s. Anchors of support were provided by a specific type of stainless steel or “of aluminum with a non-corroding material separator between the metal and stone.” These anchors are attached to the back of the panels with a rod.Finally we were able in the 1994 to achieve an appropriate and structural acceptable translucent stone veneer from granite and marble laminated in a special process to white tempered glass which makes it now possible to have the widest range of natural translucent stone suitable for interior design and exterior facades. The backlit technology if no natural light is available to enhance the beauty of all the varieties of granite and marble we have developed up to extreme thin panels of 1 mm, same as in the natural stone veneer. So nowadays we can make a backlit stoneglass panel in all sizes tailor made at a thickness of only 5 mm, all included ! Even new varieties like the hereby presented high end exclusive translucent strawberry quartz hematite.
Hans Verstappen
Sr Project manager
Packaging Detail:Wooden crates, wooden pallets , bulk |
Delivery Detail:upon order 10-30 days |